Exploring Heat Transfer in Skateboard Graphics
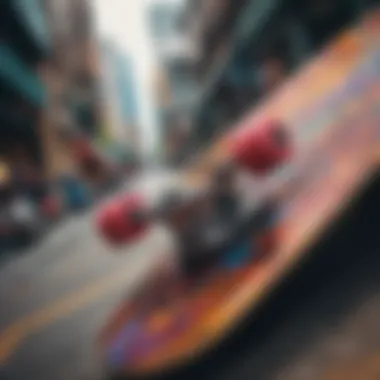
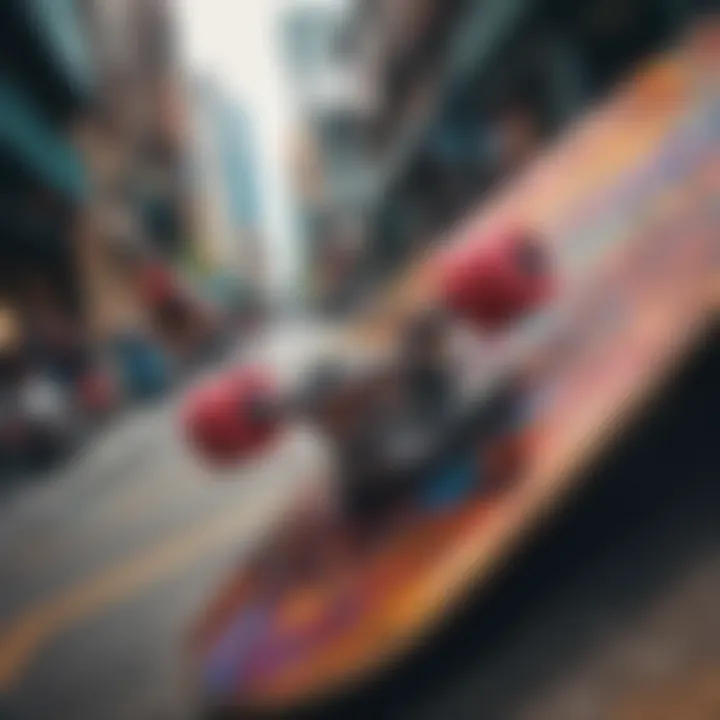
Intro
Skateboarding is much more than just a sport; it’s a form of self-expression and artistry, especially when it comes to graphics on the boards themselves. The interplay between heat transfer methods and the durable art on these boards plays a critical role in how they're not just viewed but experienced on both the streets and the half-pipes. From vibrant designs to subtle color gradients, the graphics on a skateboard serve as a canvas that reflects each skater’s personal style.
Understanding how heat transfer works in skateboard graphics goes beyond mere aesthetics. It touches on the science behind applying these vivid images through techniques like heat transfer vinyl and sublimation. The right methods can mean the difference between a design that fades after just a few rides and one that stands the test of time, enduring the wear and tear that comes with constant use.
By diving into the techniques used for applying these graphics, we'll explore how temperature and pressure influence the quality and longevity of the designs. Additionally, we will address industry standards that guide makers in the pursuit of creating not just visually appealing, but also robust skateboard graphics. This is essential knowledge, not only for manufacturers but for skaters, coaches, and parents who wish to understand what goes into the graphics of their rides.
This article aims to distill valuable insights regarding the technicalities of heat transfer in skateboard graphics while also inspiring creativity and innovation among enthusiasts who value not just the ride, but the aesthetic journey their skateboard represents.
Stay tuned as we break down the skills, techniques, and secrets behind the stunning visuals that adorn skateboard decks, making them as unique and vibrant as the skater riding them.
Prelims to Heat Transfer in Skateboard Graphics
In the vibrant world of skateboarding, graphics hold a central place. They not only beautify the skateboard but also serve as a form of expression, identity, and creativity. The way these graphics are applied, however, is crucial to their longevity and visual impact. This is where heat transfer comes into play, functioning as the bridge between artistic vision and the physical product. Understanding this topic is not just beneficial; it's essential for anyone involved in skateboard design and customizations.
Heat transfer techniques, such as vinyl transfers and sublimation printing, form the backbone of modern skateboard graphic production. Grasping the intricacies of these processes can significantly impact the quality of the graphics. For instance, improper application of heat can lead to peeling or fading. Conversely, mastering these techniques can yield striking designs that withstand the wear and tear typical in skateboarding.
Furthermore, a solid knowledge of heat transfer can also enhance safety in the sport. The choice of materials used in graphics relates directly to their durability under harsh conditions, from sunlight exposure to physical abrasion from street skating. Here, heat transfer plays a pivotal role in ensuring that the designs remain functional and appealing.
In this article, we will delve into various heat transfer methods, exploring each technique's merits and drawbacks. The intention is to furnish skaters, manufacturers, and artists with critical insights into ensuring that their graphics not only look good but also last longer. By understanding how heat affects materials and designs, one can make informed choices that marry art with functionality, creating a harmonious blend that all skateboard enthusiasts can appreciate.
Types of Heat Transfer Techniques
In the realm of skateboard graphics, understanding the types of heat transfer techniques is crucial. They serve as the backbone for applying designs to skateboards, influencing not only aesthetics but also functionality, durability, and even the skater's experience. When it comes to skateboard design, the choice of technique can significantly change the overall feel of the product. Using the right heat transfer method can elevate a plain board into an eye-catching piece of art that resonates with skaters.
Heat Transfer Vinyl (HTV)
Heat Transfer Vinyl, often known as HTV, is a popular method among skateboard graphic designers. This technique involves cutting designs out of colored vinyl and then applying heat and pressure to transfer the vinyl onto the skateboard deck. Environmental considerations are also noteworthy here; HTV can be more eco-friendly than some chemical-heavy alternatives often used in previous decades.
The application process is straightforward:
- Design Creation: Use design software to create your graphic, which is then mirrored for the vinyl cutting.
- Cutting the Vinyl: After the design is finalized, it's cut using a vinyl cutter.
- Weeding: The excess vinyl is carefully removed, leaving just the desired graphic.
- Application: Using a heat press, the vinyl is applied to the skateboard with specific settings for temperature and pressure.
While HTV can provide vibrant colors and intricate designs, it does come with its own limitations. For instance, intricate patterns might be lost if the vinyl isn't cut properly, and there's potential for peeling over time if the heat application is not precisely controlled.
Sublimation Printing
Sublimation printing is another sophisticated heat transfer technique making waves in skateboard graphics. This process is distinct as it involves dyeing the material instead of just applying a layer on top. It works beautifully on polymers or specially coated metals, commonly used in skateboard manufacturing.
To put it simply, sublimation relies on heat to turn solid dye into a gas that permeates the skateboard material, bonding the dye chemically. Here's why sublimation is gaining traction:
- Vivid Imagery: It allows for full-color, photorealistic designs without the limitations faced by traditional methods.
- Durability: As the dye becomes part of the board, it leads to long-lasting graphics that uniformly withstand the elements.
- Design Complexity: Sublimation can easily handle complex artwork with multiple colors, gradients, and fine details.
However, it's worth noting the downsides as well. The initial setup cost can be steep due to specialized equipment, and it can only be performed on specific materials. Furthermore, colors might shift slightly depending on the board's base material.
Screen Printing
Screen printing has stood the test of time as an effective and popular heat transfer method, particularly prominent in the skateboard industry. This technique utilizes a mesh screen to transfer ink onto the board where the design is applied. One of the beauties of screen printing is its adaptability—designers can use various inks, including water-based and plastisol inks, catering to different aesthetic goals.
The typical flow of screen printing involves:
- Screen Creation: Each color in a design requires a separate screen, which is prepared and coated with a light-sensitive emulsion.
- Ink Application: Using a squeegee, ink is pressed through the screen onto the skateboard deck.
- Curing: The ink is then cured using heat to ensure proper adhesion and longevity.
Advantages of screen printing include:
- Rich Color Options: It supports bold and vibrant color applications.
- Versatility: Can be used on a variety of materials and textures.
- Cost-Effectiveness: For large runs, screen printing can be more economical than other methods.
Yet, challenges persist, especially regarding detail in elaborate designs. Screen printing also has limitations related to color fidelity; as more colors are added, the cost and complexity increase significantly. Additionally, the setup and cleanup process can be labor-intensive and time-consuming.
"The choice of heat transfer technique can not only transform the aesthetic appeal of a skateboard but also defines its utility and longevity, making it a critical decision in graphic design."
In sum, each of these heat transfer techniques offers a unique blend of benefits and challenges, thus necessitating careful consideration based on the specific project requirements and intended skateboard use. Whether opting for the vibrancy of sublimation, the adaptability of screen printing, or the simplicity of HTV, understanding these processes allows designers and enthusiasts to make informed decisions, contributing significantly to the overall skateboard culture.
Heat Transfer Vinyl: Process and Applications
Heat transfer vinyl (HTV) has become a game-changer in the world of skateboard graphics. Skaters and artists alike value its ability to produce vibrant, long-lasting designs that not only catch eyes but also withstand the wear and tear typical of skateboards. This section will provide a detailed exploration of HTV, highlighting its relevance and significance in the realm of skateboard design.
Materials Used in HTV
The foundation of effective heat transfer vinyl lies in the materials that compose it. Generally, HTV is made from a type of polyurethane or polyvinyl chloride, which offers durability and flexibility. These materials make it suitable for a variety of substrates, ensuring adherence to the skateboard surface without compromising the graphics.
- Polyurethane: Known for its elasticity and tear resistance, making it ideal for dynamic skateboarding environments.
- Polyvinyl Chloride (PVC): Often used for its affordability and availability, though less flexible than polyurethane.
- Transfer Adhesive: This acts as an intermediary layer that facilitates bonding between the vinyl and the skateboard deck.
Having a sound understanding of these materials is crucial, as they directly influence the quality and longevity of the graphics.
Step-by-Step Application Process
Applying HTV to a skateboard is an art in itself. Each step must be executed meticulously to achieve the best results. Here’s how it generally unfolds:
- Design Selection: Begin by creating or choosing a design that resonates with the skateboard's aesthetics.
- Cutting the Vinyl: Use a vinyl cutter to cut the design from the HTV sheet. It's critical to remember to reverse the image to ensure it appears correctly on the skateboard.
- Weeding: This step involves removing the excess vinyl from around the design.
- Heat Application: Preheat a heat press machine to the vinyl’s recommended temperature setting. Position the cut design on the skateboard surface, then press down with controlled heat and pressure.
- Cooling and Peeling: Allow the vinyl to cool slightly before peeling away the backing paper carefully.
- Final Touch: For added durability, consider a second heat press over the design after peeling to ensure maximum adherence.
"Each of these steps contributes to the final appearance and durability of the graphics. Skipping even one can lead to less than satisfactory outcomes."
Limitations and Considerations
While HTV offers numerous advantages, it’s not without its limitations. Being aware of these may help skaters avoid potential pitfalls.
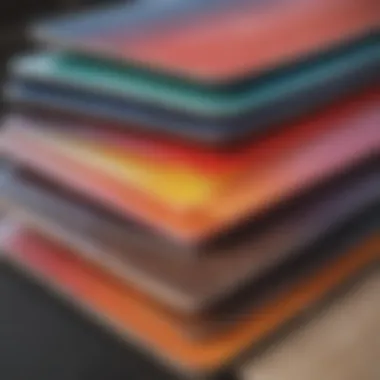
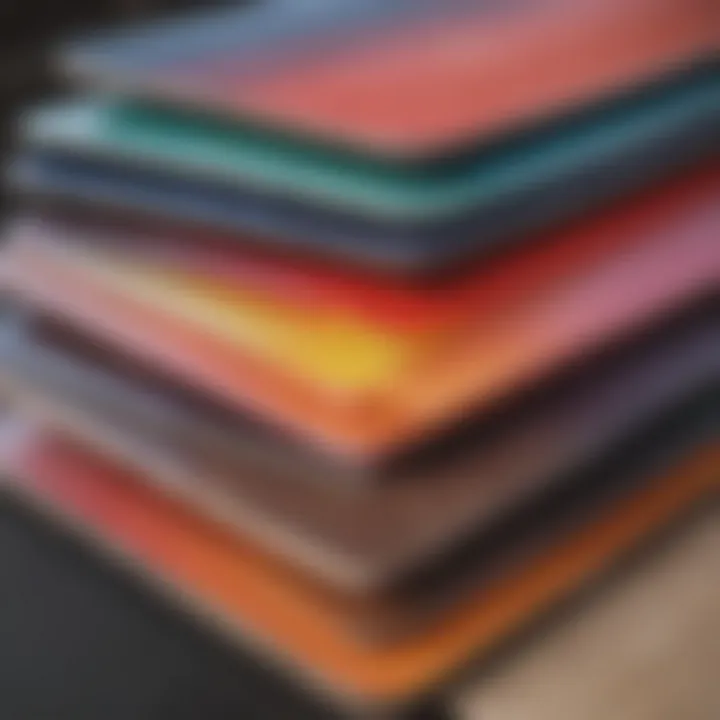
- Heat Sensitivity: The vinyl must be applied at the right temperature. Too high, and it could warp; too low, and it may not adhere properly.
- Durability Variability: Different HTV brands may vary significantly in how they perform in the face of UV exposure and friction. It’s best to conduct tests before committed application.
- Design Complexity: Intricate designs can be challenging to weed and apply accurately, which may deter some from utilizing this technique.
- Long-term Wear: While HTV is robust, it is still susceptible to peeling if not cared for properly. Regular cleaning will help maintain the graphics but avoid using abrasive materials.
In summary, while heat transfer vinyl presents a host of benefits for skateboard graphics, understanding its materials, application process, and limitations can significantly enhance the overall outcome of your designs.
Sublimation Printing: A Deeper Dive
Sublimation printing stands out as a pivotal technique in the realm of skateboard graphics, enabling artists and manufacturers to create vibrant, long-lasting designs. Unlike traditional methods, sublimation allows for the infusion of dyes directly into the material, resulting in graphics that resist fading and peeling. This deep dive into sublimation printing will uncover essential materials, the overall process, and the key advantages and disadvantages associated with this method.
Materials Required for Sublimation
Engaging in sublimation printing requires specific materials that work hand in hand to ensure a smooth application. Here’s a rundown of the critical elements:
- Sublimation Printer: Specially designed printers that utilize sublimation inks are fundamental. These printers heat the ink, transforming it into gas, which then permeates the substrate.
- Sublimation Inks: These are unique inks formulated to convert into gas when heated. The colors are vibrant and permanent, making them ideal for high-quality graphics.
- Transfer Paper: This paper holds the sublimation ink, allowing for proper transfer to the surface. Using the right type of transfer paper is important for optimal results.
- Polyester-Coated Surfaces: Since sublimation dye works best on synthetic materials, skateboard decks that are coated in a layer of polyester are often used. The polyester layer is crucial as it absorbs the ink effectively.
- Heat Press: A reliable heat press machine is essential for applying the right temperature and pressure during the sublimation process.
These materials together create an environment where colorful designs can come to life, merging art with durability.
Process Overview
Sublimation printing follows a straightforward yet precise process designed to achieve the best results. Here’s a step-by-step look:
- Design Creation: It all begins with designing the graphic on software. The design should be mirrored to ensure proper alignment during transfer.
- Paper Preparation: The design is printed on the sublimation transfer paper using a sublimation printer, making sure to utilize high heat settings.
- Surface Preparation: The skateboard deck should be cleaned and, if necessary, prepped to ensure the best adherence of the ink.
- Heat Application: The transfer paper is placed on the skateboard, followed by applying heat through a heat press. This step is where the ink sublimates, transforming from solid to gas and permeating the polyester layer.
- Cooling: After a short period, the heat is removed, and the skateboard cools, allowing the dye to settle in the surface.
This process transforms a mere blank canvas into a vibrant piece of artwork.
Advantages and Disadvantages
Understanding the pros and cons of sublimation printing sheds light on its suitability for skateboard graphics:
Advantages:
- Vibrant Colors: Sublimation creates incredibly vivid colors that resist fading over time.
- Durability: Graphics infused into the material are less likely to peel or crack, making them long-lasting.
- Soft Feel: Unlike some other methods, sublimation doesn’t add a layer on top, allowing for a smoother feel and a better grip on the board.
Disadvantages:
- Material Limitations: Sublimation works mainly on synthetic materials, which might not be preferred for all skateboards.
- Initial Costs: Investing in a sublimation printer and the required materials can be higher compared to other printing methods.
- Design Complexity: More intricate designs may require additional time and expertise to execute well.
Sublimation offers unique advantages, especially when quality and longevity matter, but the choice of material and costs can be make-or-break factors for many.
Screen Printing: Technique and Popularity
Screen printing, often known for its vibrancy and versatility, holds a pivotal role in the world of skateboard graphics. This method not only allows for high-quality prints but also caters to the unique demands of skateboard design, making it a favorite among enthusiasts and manufacturers alike. The essence of screen printing lies in its ability to reproduce complex graphics with precision and clarity, thereby enhancing the aesthetic appeal of skateboard decks.
Understanding the Screen Printing Process
The screen printing process is both an art and a science. It starts with creating a stencil on a finely woven mesh screen, which serves as a medium to transfer ink onto the skateboard surface. Here's a quick rundown of the steps involved:
- Design Creation: The first step involves crafting a design that fits the skateboard's dimensions and style. Software tools often assist in this phase.
- Screen Preparation: The selected design is then transferred onto the screen using a photosensitive emulsion. This process requires meticulous attention to detail, as even minor errors can lead to flawed prints.
- Ink Application: Once the screen is prepared, it is aligned with the skateboard. A squeegee pushes ink through the mesh, transferring the design onto the skateboard. Depending on the design, multiple screens may be needed, especially for multi-colored graphics.
- Curing: After printing, the graphic must be cured using heat, ensuring the ink adheres properly to the board.
Through these steps, what could be achieved is not just a graphic, but a statement piece that resonates with skateboard culture.
Common Uses in Skateboard Graphics
Screen printing shines in its capacity to cater to a variety of applications in skateboard graphics. Below are some common uses:
- Brand Logos: Many companies opt for screen printing to display sleek, sharp logos that can withstand the rigors of skateboarding.
- Graphic Designs: From detailed illustrations to bold patterns, screen printing can handle a wide range of designs, making it suitable for custom and limited edition decks.
- Collaborations: Artists often partner with brands to create unique graphics using screen printing, ensuring that the artistry resonates with the target audience.
Moreover, its durability means that graphics don't easily fade or peel, a crucial factor for skaters who want their boards to look fresh.
Challenges Faced in Screen Printing
Even though screen printing boasts numerous advantages, it doesn’t come without its challenges. Here are some obstacles faced during this process:
- Setup Time and Cost: Preparing the screens and inks can be time-consuming and requires an initial investment, particularly for custom jobs.
- Design Limitations: While it excels in producing bold colors, intricate designs may lose some detail due to the nature of the printing process. This is especially true for small text or complex gradients.
- Material Compatibility: Not all skateboard materials work well with screen printing. Certain finishes can affect how ink adheres, demanding careful consideration of material choices before printing.
Materials Impacting Heat Transfer Quality
The topic of materials impacting heat transfer quality plays a pivotal role in the creation and longevity of skateboard graphics. Understanding how different materials interact during the heat transfer process gives artists and manufacturers a leg up in producing graphics that not only look stunning but also stand the test of time.
When it comes to heat transfer, it’s not just about slapping some graphic onto a skateboard and calling it a day. The successful application of graphics relies heavily on the interplay of materials used at each step. The right choice can make the difference between a vibrant design that holds up against the elements and one that fades quicker than you can say "kickflip."
Types of Plastics Used in Skateboards
Plastics serve as a backbone in skateboard construction, and their varieties bring unique traits that directly affect graphic quality. For instance, polypropylene is often used in some skateboards due to its lightweight nature, but its smooth surface can sometimes create challenges for adhesion, especially for heat transfer applications. In comparison, materials like ABS (Acrylonitrile Butadiene Styrene) provide better surface texture for better graphic adhesion and heat distribution.
Moreover, the density and thermal properties of plastics influence the way heat is absorbed. A skateboard deck made from high-density polyethylene might retain heat differently than one made from a composite material.
Adhesives and Their Role
Adhesives are the unsung heroes of the graphic application process. They work to create a bond between the graphic and the skateboard surface, ensuring that designs stick and remain intact even during rigorous use. Not all adhesives are born equal, though. Some react poorly to heat, while others excel at withstanding extreme temperatures.
A common adhesive used in HTV, for example, is a polyurethane-based option that exhibits exceptional heat resistance and flexibility. This is paramount for skateboards, as the board is subjected to various stresses while in use. Selecting the right adhesive often involves considering factors like heat resistance, moisture exposure, and flexibility.
"In the world of skateboarding, a graphic may look great but without the right adhesive, it could peel off faster than a bad penny."
Ink Characteristics
Quality ink characteristics are equally crucial for achieving an enduring graphic. The formulation of the ink affects how it reacts to heat when being transferred. Water-based inks, for instance, may dry quickly but can lack the colorfastness needed for outdoor exposure.
• Pigment Types: The choice between pigment-based and dye-based inks can make a difference. Pigments often offer better UV resistance, making them more suitable for graphics that will be exposed to sunlight. • Viscosity: Thicker inks might require more heat for effective transfer, while thinner inks can lead to smudging if not handled carefully.
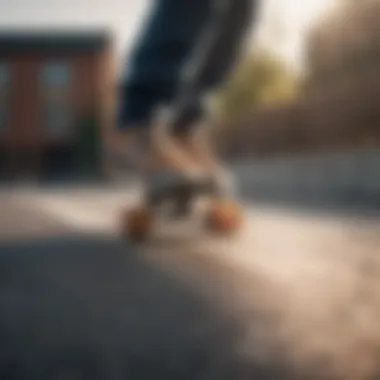
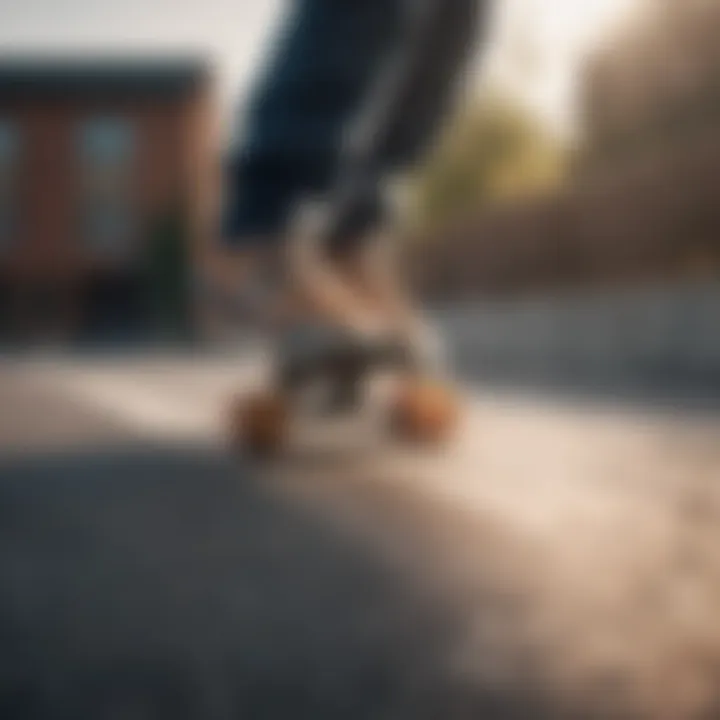
In essence, the selection of inks should reflect the intended use of the skateboard and the visual effects desired. Knowing the intricacies of these materials allows designers to merge creativity with functionality, leading to standout pieces that speak volumes about the skater’s personality.
By delving into these materials and understanding their characteristics, skateboard enthusiasts can make informed decisions that enhance both the artistry and durability of skateboard graphics.
Design Principles for Effective Graphics
In the world of skateboarding, graphics are more than just a flashy visual. They encapsulate a skater's personality, influence brand identity, and can even affect performance. As skateboard graphics continue to evolve, understanding the design principles that underpin effective graphics becomes crucial for both manufacturers and artists. The right design achieves a balance between aesthetics and functionality, draws on color theory sensibly, and resonates with consumers on a deeper level, making it an integral part of skate culture.
Balancing Aesthetics with Functionality
Skateboards endure extreme conditions. They are subjected to friction, varying temperatures, and diverse weather. Designers should prioritize not only how appealing the graphic looks but also how well it retains its integrity under stress.
- Durability: A graphic needs to be tough enough to withstand scratches and wear. Selecting the right materials for the print, such as high-quality inks, can help ensure longevity.
- Grip and Performance: The placement and texture of graphics might impact performance. Some designs may affect grip tape application or how the board interacts with the ground. For instance, a slick finish can interfere with grip, so balancing glossy designs with practicality is key.
"A great skateboard graphic marries art and physics—looking good while also working well under pressure."
Color Theory in Skateboard Graphics
Color is not just about aesthetics; it’s a powerful language that communicates brand identity and a skater's style. Choosing the right palette can evoke emotion and set a mood.
- Warm vs. Cool Colors: Warm colors such as reds and yellows can create energy and excitement, which might appeal to younger skaters. Cool colors like blues and greens can exude calmness and stability.
- Contrast and Visibility: High contrast combinations not only catch the eye but also enhance legibility. This becomes especially important for logos or branding elements that need to stand out.
- Cultural Significance: Certain colors may hold different meanings and associations in various cultures, which can be pivotal for a brand seeking to connect with a global audience.
Incorporating Brand Identity
Brand identity in skateboard graphics involves much more than just icons or logos. It’s about creating a consistent visual narrative that resonates with the target audience and cultivates a community.
- Consistency: Regularly utilizing distinct colors, fonts, and styles can reinforce brand recognition. A skateboarder should be able to identify a brand at a glance, perhaps even from a distance.
- Storytelling: Each graphic offers a chance to tell a story. Artists often weave narratives that reflect the values or history of the brand, elevating the artwork beyond mere decoration.
- Connection with Community: Engaging with skaters through social media and events, while highlighting the graphic design process, fosters a sense of belonging. For many skaters, their boards are an extension of their identity—and graphics play a key role in that narrative.
The Role of Heat in the Transfer Process
The significance of heat within the transfer process for skateboard graphics can’t be overstated. It’s not merely a matter of applying a graphic and hoping for the best; it’s a critical component that directly influences the success of the final product. Heat initiates the transformation of materials, ensuring adherence and longevity while shaping aesthetic appeal. The success of any graphic application hinges on understanding the appropriate temperature and pressure, transforming how we see and interact with skateboard designs. This section delves into each of these elements.
Temperature Control
Temperature control is fundamental in ensuring that graphics adhere properly to skateboards without damaging the underlying materials. When applying heat transfer techniques, such as HTV or sublimation, the temperature needs to be calibrated to match the specific requirements of the materials involved. For instance, using a heat press requires precision; typically, temperatures range from 320°F to 400°F (approximately 160°C to 200°C).
A misstep here can lead to issues like bubbling, where heat causes air pockets to form beneath the graphic, or scorching, where the heat damages the surface finish of the skateboard.
- Key considerations for temperature control:
- Material compatibility: Different materials react to heat differently. For example, many plastics used in skateboards have specific heat tolerances.
- Monitoring heat: A reliable thermometer is essential. User error often comes from not accurately tracking heat levels during application.
- Calibration: Prior testing may be necessary to set the ideal temperature before mass production.
Pressure Application
Along with temperature, pressure plays a pivotal role in the outcome of heat transfer techniques. It is not sufficient to heat a graphic; applying appropriate pressure ensures that the graphic bonds to the surface uniformly. Too little pressure can lead to incomplete adhesion, while excessive pressure can damage the material beneath.
- Methods of pressure application:
- Effects of inadequate pressure:
- Manual presses: Common in smaller operations, these allow for flexibility but require careful exertion.
- Heat presses: These machines provide even pressure across the surface, making them ideal for larger production runs.
- Peeling graphics: Without adequate pressure, graphics may start to lift after use.
- Poor alignment: Incorrect application can lead to misaligned graphics, ruining the aesthetic appeal of the skateboard.
Impact on Longevity and Quality
The ultimate longevity and quality of a skateboard graphic are directly affected by the interplay of heat and pressure during the transfer process. A well-executed graphic application not only enhances visual appeal but ensures that the design withstands the rigors of skateboarding.
"Quality craftsmanship in skateboard graphics means considering every factor, from heat to pressure; it’s where art meets durability."
Graphics that are applied under ideal conditions are less likely to fade, peel, or crack over time. This is particularly important for professional skateboarders who rely on their boards for both performance and brand representation.
- Factors to enhance longevity:
- Quality materials: Investing in high-quality inks and graphics ensures that the designs are robust against wear and environmental factors.
- Proper application techniques: Following temperature and pressure guidelines ensures that each graphic will last longer, reducing the need for constant reapplication.
Industry Standards in Graphics Production
Understanding industry standards in graphics production is key for achieving excellence in skateboard graphics. These standards ensure that the graphics not only look good but also hold up under the pressures of use, weathering, and time. For skateboard manufacturers and artists alike, adhering to these standards can mean the difference between a fleeting trend and a lasting classic.
Regulatory Guidelines
When it comes to producing skateboard graphics, following regulatory guidelines is no small feat. These regulations might include safety standards (like those from ASTM International) and environmental compliance, especially as more companies aim to lessen their carbon footprint. For instance, using non-toxic inks and sustainable materials is gaining traction as part of an overarching effort to promote eco-friendliness in the industry.
Key aspects of regulatory guidelines involve:
- Material Safety: Ensuring that all materials used are safe for both the artist and the end user.
- Labeling: Clear labeling on products helps consumers make informed choices, especially regarding harmful substances.
- Environmental Standards: Adapting practices to comply with local and international regulations regarding waste management, recycling, and emissions.
Emphasizing compliance not only fulfills legal requirements but also enhances brand trust. A manufacturer who demonstrates a commitment to these standards often earns loyalty from consumers who prioritize ethical and safe production practices.
Quality Assurance Practices
Quality assurance practices are the backbone of effective graphics production. These are the checks and balances that ensure every skateboard produced meets high standards. Without these practices, the risk of defects and inconsistencies rises, leading to diminished brand reputation.
To maintain quality, several practices should be implemented:
- Testing Materials: Prior to production, testing the inks, adhesives, and substrates ensures they perform well under stress.
- Process Audits: Regular audits of production processes help identify potential issues early, preventing costly mistakes down the line.
- Feedback Loops: Encouraging feedback from skaters about the graphics helps manufacturers understand real-world performance and allows them to make adjustments accordingly.
Incorporating these quality assurance practices can greatly influence the durability of skateboard graphics. A graphic that’s been rigorously tested and vetted is far more likely to withstand the elements and rough usage that skaters put their decks through.
Adhering to industry standards isn’t just about compliance—it shows a commitment to quality that resonates with consumers.
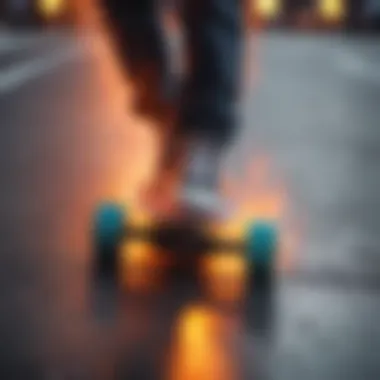
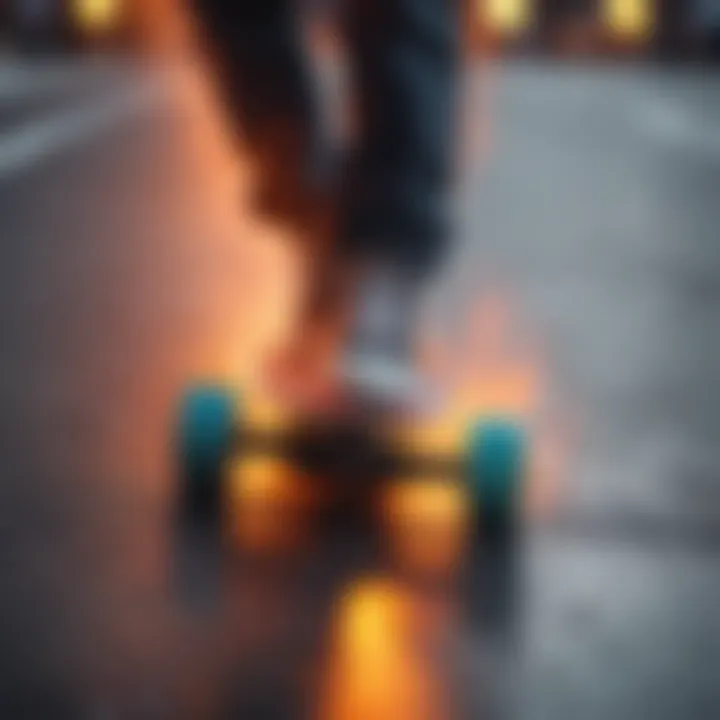
Impact of Environmental Factors on Graphics
The environmental factors greatly influence skateboard graphics, making it pivotal to understand how they interact with the materials and processes involved in heat transfer. These conditions, from weather variations to exposure to sunlight, can determine the longevity and visual appeal of the designs skaters treasure.
Weather Considerations
Weather plays a hefty role in determining how skateboard graphics hold up over time. Rain, humidity, and temperature fluctuations can all impact the integrity of graphics due to the stress they place on the materials used.
- Rain and Moisture: Water exposure can cause inks and adhesives to break down, leading to peeling or distortion of graphics. For instance, skateboards that are regularly used in damp environments might see their prints fade much quicker than those kept dry.
- Temperature Variations: Hot and cold weather can affect both the application process and the durability of graphics. For example, applying vinyl graphics in extreme heat can lead to bubbles and misalignment. Conversely, cold weather can cause the adhesives to set improperly.
"Understanding local weather conditions can be the difference between a vibrant graphic and a faded piece of art on your skateboard."
Being aware of these considerations allows manufacturers and skaters to make informed choices about how to best protect and maintain their skateboard art.
UV Exposure and Fading
Ultraviolet (UV) rays from the sun present a significant challenge for skateboard graphics. Over time, prolonged exposure to UV light can cause discoloration and fading, stripping the visuals of their original luster. Here are a few aspects to consider:
- Types of Inks: Not all inks are created equal when it comes to UV resistance. Some may be designed to withstand more intense sunlight, while others, especially cheaper options, can quickly lose color.
- Protective Coatings: Applying a UV-resistant clear coat can offer a layer of protection, reducing the risk of fading. This additional step may increase the durability of graphics, especially for decks frequently left outside or exposed to direct sunlight.
- Storage Practices: Proper storage of skateboards—such as keeping them out of sunlight when not in use—can extend the life of graphics significantly.
To wrap it all up, considering the environmental factors at play can dramatically influence the way skateboard graphics are maintained and experienced. Taking proactive steps helps to ensure that these designs not only resonate with aesthetic appeal but also last longer on the streets or in the skate parks.
Unique Case Studies in Skateboard Graphics
Understanding unique case studies in skateboard graphics is like peeking behind the curtain where art, culture, and technology merge. These case studies not only illustrate how diverse the design landscape is but also underscore the important role that heat transfer techniques play in the success of these projects. Artists and brands often employ various printing methods that deliver not just aesthetic value but also longevity and performance—qualities that ardent skateboarders prioritize.
In today’s fast-paced realm of skateboard culture, standing out can be a make-or-break scenario. Unique cases help explore how creativity and technical proficiency intersect, shedding light on the innovative approaches artists and manufacturers take to distinguish their work.
Artist Collaborations
Collaborative projects between artists and skateboard companies have revolutionized the way graphics are applied and perceived. Take, for example, the renowned collaboration between the legendary artist Shepard Fairey and the skateboard brand Almost. By integrating his signature street art style with heat transfer vinyl techniques, this collaboration created not only visually striking boards but also a cultural commentary.
Often, these collaborations involve extensive back-and-forth, ensuring the final product resonates with both the artist's vision and the skateboard's performance needs.
- Benefits of Collaborations:
- Increases visibility for both artists and brands.
- Merges artistic expression with practical design considerations.
- Elevates the perceived value of the skateboard, appealing to collectors and enthusiasts alike.
However, it’s crucial to consider that not all collaborations run smoothly. Misalignment in vision or production processes can lead to products that fail to resonate. It highlights the importance of compatibility between the artist's artistic goals and the brand’s mission in achieving a successful outcome.
Limited Edition Releases
Limited edition skateboard graphics often capture the essence of exclusivity and desirability. These products typically feature intricate designs and unique themes that reflect particular moments or cultural phenomena.
For instance, the introduction of a limited-edition board by PLAN B Skateboards featuring art from the late artist Keith Haring was an instant success. The use of sublimation printing for these lines strengthend both the durability of the graphics and the vividness of the colors, making the boards ideal for display and use alike.
A limited release creates a sense of urgency among buyers, leading them to act faster than they would for standard production boards.
- Key Considerations for Limited Editions:
- Binding the graphic design to cultural or social themes can enhance relevance.
- Knowing your audience is key; understanding what resonates can drive sales.
- Production constraints need to be balanced with marketing strategies to avoid overproduction or underwhelming launches.
Moreover, these limited editions generate excitement within the skateboarding community, leading to increased conversation around the techniques used. This excitement also helps expose newer technologies and methodologies in heat transfer processes, pushing the envelope on what is possible in skateboard graphics.
In summary, case studies of artist collaborations and limited edition releases provide rich insights into the artistic process and consumer engagement, showcasing how heat transfer techniques are used to amplify creativity while serving the practical demands of skateboard performance.
Future Trends in Skateboard Graphics
The landscape of skateboard graphics is rapidly evolving. As technology advances, so do the methods and mediums used to create the striking visuals that adorn skateboard decks. Understanding these future trends is essential for artists, manufacturers, and skateboard enthusiasts alike. This section dives into how advancements in printing technology and sustainability considerations are shaping the future of skateboard graphics.
Advancements in Printing Technology
In the realm of skateboard graphics, the arrival of cutting-edge printing technologies is a game changer. Innovations like digital printing and direct-to-board printing are blending creativity with precision. Unlike traditional methods, these new techniques offer vast color palettes and intricate designs without compromising durability.
One of the most significant advantages of digital printing is its ability to create complex imagery that mimics photographs and detailed art styles. Artists can explore their creativity without the limitations often imposed by older practices.
For instance, digital print bonding allows for a deeper infusion of inks into the skateboard surface, resulting in vibrant colors that resist peeling or fading over time. The speed at which artists can now produce customized decks has also increased, making it feasible for small operations to keep up with demands for limited editions.
However, the costs associated with these technologies can be a hurdle for smaller brands. It is crucial for companies to balance quality with affordability to remain competitive, particularly in a marketplace that values both artistry and accessibility.
Sustainability Considerations
As environmental concerns grow, skateboard graphic production is facing pressure to adapt. The integration of eco-friendly practices is no longer a bonus; it's becoming a necessity. By prioritizing sustainable materials and methods, manufacturers can significantly reduce their ecological impact.
For instance, using water-based inks instead of solvent-based alternatives can greatly diminish the use of harmful chemicals. Likewise, sourcing sustainable woods and adhesives can ensure that the entire deck production process is less taxing on the environment.
This shift not only appeals to environmentally conscious consumers but also fosters a brand image committed to social responsibility.
Implementing sustainability practices does come with challenges. There's an educational gap regarding materials and methods available, making it vital for producers to stay informed. Collaborations with environmental agencies can also help in navigating these waters, ensuring that practices align with best standards in sustainability.
"Ultimately, the goal is clear: to merge creativity with responsibility, making sure that our love for skateboarding does not come at the cost of our planet."
Closure: Merging Art with Functionality
The intersection of artistry and functionality is an essential theme in the realm of skateboard graphics. This article has dissected the various technical processes involved in heat transfer techniques while simultaneously appreciating the vital role of creativity in design. By blending these elements, we can fully understand how aesthetics enhance not just the visual appeal, but also the overall performance of skateboard graphics.
Key Elements of Merging Art with Functionality
- Technical Mastery: Knowledge of heat transfer methods—like HTV, sublimation, and screen printing—shows how crucial temperature and pressure adjustments are to achieving optimal results. Applying the right technique not only ensures vivid graphic representation but also contributes to the durability of designs as skaters grind down the streets.
- Material Impact: The selection of appropriate materials affects both the visual and functional properties of skateboard graphics. For example, using high-quality inks and substrates can ensure that colors remain vibrant longer when exposed to environmental challenges such as UV rays or moisture. This becomes a critical consideration for anyone involved in skateboard design, especially manufacturers who aim to balance aesthetics with practicality.
- Creative Expression: Effectively merging aesthetics and functionality allows for unique artistic expressions. When artists collaborate with designers, they can create visually striking pieces that also meet the demands of skate performance. This synergy can lead to limited edition designs, boosting a brand's appeal and cult following among enthusiasts.
- Industry Standards: Adhering to established quality assurance practices and regulatory guidelines is not just about compliance, but it fosters trust and credibility in the market. High standards in production chemistry and heat application techniques ensure that consumers receive products worth their investment; it becomes less about quantity and more about quality.
- Sustainability: Addressing sustainability in design practices is more pertinent now than ever. Utilizing eco-friendly materials without compromising graphic quality represents the next frontier in skateboard graphics. It demonstrates a conscientious approach toward our environment while maintaining a strong aesthetic appeal.
"Graphics don’t just decorate a board; they tell a story, represent a culture, and embody dreams."
In summary, merging art with functionality in skateboard graphics leads to not only enhanced visual experiences but also contributes to a product's longevity and performance. Understanding these principles equips skaters, artists, and manufacturers alike with the insights necessary to innovate while respecting the board's primary purpose.
Final Thoughts on Heat Transfer and Creativity
Heat transfer serves as a bridge between technical skill and artistic vision. Each method discussed reveals its own set of challenges and opportunities. For instance, if someone chooses sublimation over screen printing, they embrace a different palette of possibilities driven by the very nature of the materials involved.
Yet, amidst these technicalities, the essence of creativity must shine through. Every graphic tells a story—often reflecting local culture, personal journeys, or the spirit of skateboarding itself. In this world, creativity is not bound by convention but flows freely, echoing the movements of skaters who dare to push boundaries.
Ultimately, understanding heat transfer isn’t just for enthusiasts or manufacturers; it's also for artists who want to empower their visuals through informed choices. The marriage of art and technology results in vibrant designs that resonate with a diverse audience, ensuring skating remains not just a sport, but a lifestyle that thrives on individuality and artistic expression.